Just How Metal Stamping is Revolutionizing the Automotive and Aerospace Industries
Wiki Article
Advanced Techniques in Steel Stamping for Accuracy Manufacturing
In the realm of accuracy manufacturing, the advancement of metal marking methods has been a pivotal pressure in achieving unrivaled degrees of accuracy and performance. As markets continually require finer resistances and intricate layouts in their metal parts, the quest for innovative methods in steel stamping has actually magnified. From the application of advanced multi-stage marking processes to the combination of cutting-edge automation innovations, the landscape of steel stamping is undertaking a profound improvement. In this dynamic field, the merging of innovation and precision is improving the possibilities of what can be accomplished in steel fabrication.Advanced Multi-Stage Stamping Processes
Going over the details of advanced multi-stage stamping processes reveals the advanced methods utilized in contemporary production techniques. Metal Stamping. Multi-stage marking is an intricate procedure that involves multiple steps to change a level sheet of steel right into a last stamped item. Using dynamic passes away, where various procedures are executed at each phase of the marking procedure, permits high precision and effectiveness in the manufacturing of elaborate metal partsDuring the initial phases of multi-stage marking, the flat metal sheet is fed into the stamping press, where a collection of passes away are utilized to cut and shape the material. Subsequent stages entail added creating, flexing, and punching operations to further refine the component. Each phase is very carefully created to build on the previous one, resulting in the creation of complex geometries with limited resistances.
Advanced multi-stage stamping procedures call for a high level of experience and accuracy to guarantee the quality and uniformity of the stamped components. By utilizing innovative equipment and tooling, producers can produce a wide variety of metal parts with effectiveness and accuracy.
Accuracy Tooling Innovations
Precision tooling developments have actually reinvented the metal marking industry, improving performance and top quality in producing processes. These innovations have actually considerably impacted the means metal parts are created, leading to greater precision and uniformity in the end products. One essential technology is the advancement of computer system numerical control (CNC) modern technology in tooling design and manufacture. CNC systems permit detailed designs to be equated straight into tooling, making certain accuracy and repeatability in the marking procedure.Additionally, the combination of sensing units and real-time surveillance capacities in accuracy tooling has actually made it possible for manufacturers to spot and attend to issues quickly, lessening downtime and minimizing scrap prices. By integrating wise innovation into tooling, operators can enhance parameters such as pressure, speed, and alignment throughout the marking procedure, leading to enhanced product quality and increased productivity.

Automation in Metal Stamping
The evolution of precision tooling innovations in the steel marking market has paved the way for significant innovations in automation, changing the production landscape towards enhanced efficiency and performance. Metal Stamping. Automation in steel stamping involves the use of innovative equipment and robotics to carry out different jobs commonly carried out by human drivers. This shift towards automation supplies many benefits, including boosted accuracy, faster manufacturing cycles, and decreased labor costsOne trick aspect of automation in steel marking is the implementation of computer system numerical control (CNC) systems, which enable exact control over the stamping procedure. CNC innovation allows for the development of complex and detailed metal components with constant top quality. Furthermore, automated systems can be programmed to run constantly, leading to greater output prices and much shorter lead times.
Moreover, automation improves workplace safety and security by reducing hands-on handling of hefty materials and lessening the risk of mishaps (Metal Stamping). click As making industries proceed to welcome automation, the future of metal stamping holds excellent promise for even better efficiency and advancement
High-Speed Stamping Strategies
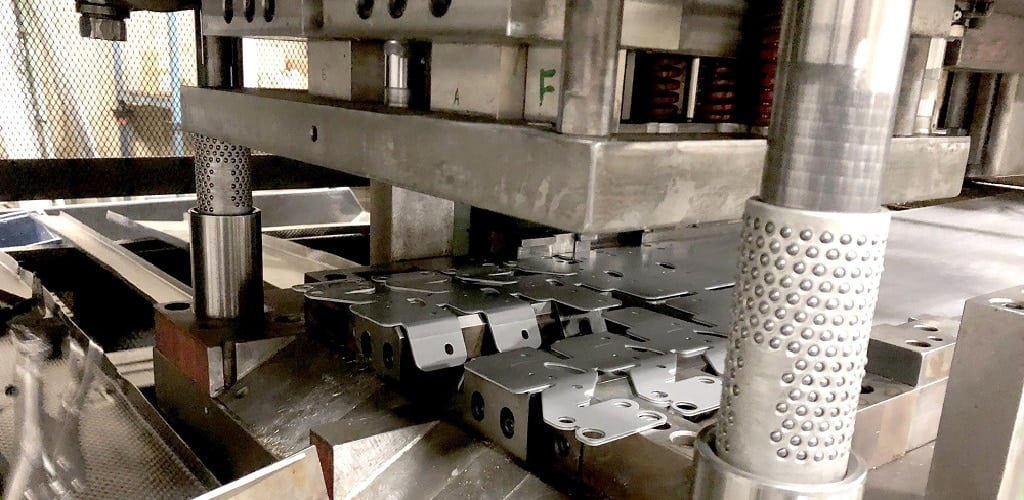
One of the primary advantages of high-speed stamping techniques is the ability to create a big volume of parts in a shorter amount of time compared to conventional stamping techniques. This boosted performance not only allows producers to fulfill limited production deadlines however likewise allows cost savings through economies of range. In addition, high-speed marking can aid minimize material waste by optimizing the material use throughout the stamping process.
Furthermore, high-speed marking strategies usually include ingenious functions such as quick die adjustment systems and real-time surveillance abilities, even more enhancing the total effectiveness and versatility of the metal marking procedure. As innovation remains to advance, high-speed stamping is anticipated to play navigate to this site a vital function in driving the future of precision production.
Quality Assurance in Stamping Workflow
Effective top quality control actions are necessary for making sure the dependability and consistency of metal marking procedures. Quality assurance in stamping procedures involves a collection of systematic procedures aimed at spotting and preventing flaws in the manufactured parts. One essential facet of quality assurance in steel stamping is using sophisticated inspection strategies such as optical evaluation systems and coordinate gauging devices (CMMs) to validate the dimensions and resistances of stamped parts.Furthermore, quality control steps in marking operations commonly include the application of analytical process control (copyright) methods to keep an eye on the production process in real-time and make certain that it stays within appropriate limits. By assessing data and determining fads, manufacturers can proactively deal with any kind of discrepancies from the preferred top quality requirements.
Moreover, quality assurance in metal stamping operations likewise entails thorough material testing to make certain that the raw materials made use of meet the called for specs for the stamping procedure. This might consist of performing product solidity examinations, tensile toughness examinations, and dimensional inspections to guarantee the quality and integrity of the stamped components. In general, carrying out robust quality assurance procedures is critical for attaining high-grade stamped components continually.
Verdict
In verdict, progressed strategies in steel stamping play an important function in precision manufacturing procedures. Via multi-stage marking processes, innovative tooling options, automation, high-speed methods, and extensive quality assurance steps, manufacturers can achieve greater levels of accuracy and performance in their procedures. These improvements in metal stamping modern technology have actually enabled companies to generate complicated parts with limited resistances, inevitably causing improved item high quality and customer satisfaction in the production market.Report this wiki page